WHY DESIGN/BUILD?
Unlike traditional building practices which divide responsibilities for design efficiency, economy and
construction among architects, engineers and contractors, the Design/Build approach assigns total
responsibility for efficiency and control to a single organization.
This modern management practice allows a single source to balance good design with construction economy.
And because it does not fragment the building process by separating design from construction, it permits
better and tighter control of quality, cost and construction duration. By applying the efficiency and
control of modern management, it encourages the designer/builder to seek the best and most economical
way to build, consistent with the owner's objectives. It also allows the owner to seek professional
guidance and secure cost estimates at the concept stage without incurring the expense and commitment
of conventional building methods.
Thus, the designer/builder can take the owner's ideas and needs and provide a complete package of design,
estimates, drawings, schedules and construction.
A typical Design/Build time-table would include the following steps:
1. INITIAL CONFERENCE- Discussions between owner and designer/builder establishing needs,
parameters, etc.
2. ROUGH SKETCH- Preliminary sketches prepared and submitted to owner for his review, evaluation and revisions.
3. BUDGET ESTIMATE- Submitted with rough sketch. Usually accurate to within 5% of final cost.
4. CUSTOMER ACCEPTANCE- Plans and estimates are approved. Contract for Design/Build is signed.
5. WORKING DRAWINGS- Final drawings, including all architectural and engineering details are prepared
and submitted to owner for approval prior to construction.
6. CONSTRUCTION START- Upon approval of working drawings, building permits are secured and construction begins.
7. CONSTRUCTION FINISH- Building is completed, certified acceptable and turned over to owner.
STEEL - The Better Way To Build
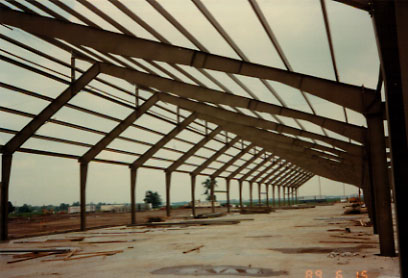
Pre-engineered steel buildings are unique in many ways and offer owners significant advantages over more
conventionally built structures.
ECONOMICAL
Because they use factory produced components, steel buildings usually have a lower initial cost than conventional structures.
But the savings don't stop there. Roofs are virtually indestructable and should last the lifetime of the building without
deterioration. Long-wearing factory coated finishes reduce or eliminate painting maintenance. Structural
deterioration, cracks, damp rot and insect damage are also eliminated. Thus, the per year cost of your steel building will
be considerably less than a comparable building of conventional construction.
PERMANENT
Steel buildings are built to last. In Florida they are engineered to withstand hurricane force winds and meet or exceed
the stringent Stand Building Code.
INSULATION
Steel buildings can be easily and effectively insulated for efficient, cost-reducing heating and cooling. In most instances,
insulated steel buildings will have a better insulating value than conventional cement block structures.
PREDICTABLE CONSTRUCTION SCHEDULE
There's no guesswork on steel building construction. While the building components are being fabricated in the factory,
our engineers and field personnel prepare the site and foundation, ready for erection of the components upon
delivery. In virtually every instance, total elapsed time from concept to occupancy is faster
than using conventional methods.
FLEXIBLE
Steel buildings can be designed for any size, for any use. They are particularly well suited for wide roof spans and the
savings for such structures (over conventional construction) actually increases with the span itself. Expansion
of existing structures is relatively easy and usually very economical. Typically, a metal building can be
enlarged by removing the end or side wall panels, erecting additional framework and adding matching wall
and roof panels. In most cases, the original wall panels can be re-used.
|